Pressure is a key component in complying with the Environmental Protection Agency’s Underground Injection Control Class VI Program, both showing that injection pressure is less than the permitted maximum and that the area of pressure elevation is within the prepared and permitted Area of Review Most wells are instrumented with pressure and temperature gauges in the wellhead or flow line that may be recorded by a technician or transmitted to a central location. Because CO2 density varies strongly with temperature and pressure, pressure and temperature sensors located near the injection interval reduce uncertainty in measuring this key parameter. The value of the pressure signal can be enhanced by changing injection rates and observing the response of the reservoir. Changes in pressure response can be indicative of loss of containment in the well or reservoir. Gauges open to zones above the injection zone may be useful for detecting CO2 release through the geologic seals. Downhole pressures and temperatures can also be used as inputs for models to better predict the migration of injected CO2. Pressure and temperature transducers may be temporarily or semi-permanently placed within the wellbore, or they may be permanently attached to the outside of the casing.1National Energy Technology Laboratory. (2017). Best practices: Monitoring, verification, and accounting (MVA) for geologic storage projects. National Energy Technology Laboratory, U.S. Department of Energy. https://netl.doe.gov/sites/default/files/2018-10/BPM-MVA-2012.pdf
Summary of Pressure and Temperature Monitoring
- Description: A large array of gauges is available to measure pressure and temperature. Technology is mature. Gauges are deployed at wellhead and can be permanently installed on casing, semi permanently deployed on tubing, or intermittently emplaced on slickline. Wireline communications are standard with the casing and tubing deployments; the intermittent emplacement may either be on wireline or use internal memory and be retrieved. Gauges may be deployed both on injection wells and on monitoring wells distant from injection intervals.
- Benefits: Reservoir pressure is a key parameter in the Environmental Protection Agency’s Underground Injection Control Class VI Program, and because of the complex temperature and pressure effects on fluid density, direct measurements at the reservoir may be needed to augment and calibrate standard wellhead pressure measurements. Measurements of reservoir response to changes in injection pressure is a mature tool for assessing fluid flow and hydrologic properties and is a key input for history-matching simulation models.
- Challenges: Gauges must be in communication with the reservoir. If the gauge is run inside of the casing, then the well must be perforated and thus the entire well is potentially exposed to corrosive fluids, increased pressure, and potential changes in wellbore fluids that may alter monitoring technologies run from inside of it (e.g., seismic). Gauges run outside of casing are not retrievable, must be carefully placed to exclude cement between the gauge and the reservoir, and must have a line back to the wellhead that could be a potential leakage path.2National Energy Technology Laboratory. (2017). Best practices: Monitoring, verification, and accounting (MVA) for geologic storage projects. National Energy Technology Laboratory, U.S. Department of Energy. https://netl.doe.gov/sites/default/files/2018-10/BPM-MVA-2012.pdf
Application
In July 2008, Denbury, an oil and gas operator, began CO2-enhanced oil recovery (EOR) operation at the Cranfield Oil Field located 20 km east of Natchez, Mississippi. Through funding from the U.S. Department of Energy, a number of research partners were able to deploy a variety of monitoring technologies focused on a commercial CO2 injection environment at the site. The Cranfield Project safely demonstrated large-scale, long-term CO2 injection and storage in a CO2-EOR and associated saline reservoir between 2009 and 2015, during which time 5,371,643 t of CO2 were successfully stored.3National Energy Technology Laboratory. (n.d.). Cranfield Project: Lower Tuscaloosa Formation, Natchez, Missippipi Southeast Regional Carbon Sequestration Partnership. Retrieved July 1, 2021, from https://www.netl.doe.gov/sites/default/files/2018-11/Cranfield-Project.PDF4Lu, J., Kordi, M., Hovorka, S. D., Meckel, T. A., & Christopher, C. A. (2013). Reservoir characterization and complications for trapping mechanisms at Cranfield CO2 injection site. International Journal of Greenhouse Gas Control, 18, 361-374.
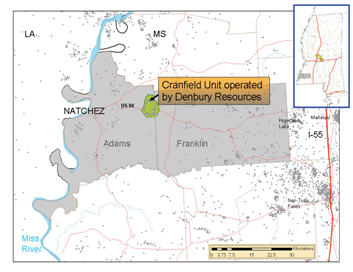
Location of the Cranfield Project east of Natchez, Mississippi. The yellow highlighted area in the inset map of Mississippi is the location of Jackson Dome, the source of the CO2 injected at Cranfield.5National Energy Technology Laboratory. (n.d.). Cranfield Project: Lower Tuscaloosa Formation, Natchez, Missippipi Southeast Regional Carbon Sequestration Partnership. Retrieved July 1, 2021, from https://www.netl.doe.gov/sites/default/files/2018-11/Cranfield-Project.PDF
At the time of the project, the Cranfield site features the larges suite of monitoring, verification and accounting technologies all focused on one spot.6National Energy Technology Laboratory. (n.d.). Cranfield Project: Lower Tuscaloosa Formation, Natchez, Missippipi Southeast Regional Carbon Sequestration Partnership. Retrieved July 1, 2021, from https://www.netl.doe.gov/sites/default/files/2018-11/Cranfield-Project.PDF The project tested feasibility of a first-of-its kind above-zone monitoring interval (AZMI) concept for geologic storage. The premise of AZMI pressure monitoring is that fluids leaking out of the injection zone would be at pressure higher than that of hydrostatic fluids in overlying permeable units; therefore, if the leakage flow path is in contact with the overlying units, fluids will enter them and elevate pressure monitored by gauges in the well.7Hovorka, S. D., Meckel, T. A., & Trevino, R. H. (2013). Monitoring a large-volume injection at Cranfield, Mississippi—Project design and recommendations. International Journal of Greenhouse Gas Control, 18, 345-360.
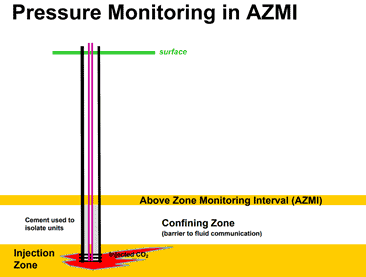
Monitoring pressure in an above-zone monitoring interval (AZMI) is a method to assess retention in the injection zone. At Cranfield, pressure was monitored above the confining zone in the Above Zone Monitoring Interval (AZMI), approximately 120 m above the injection zone.8Hovorka, S. (2012, September 21). What to do about CO2: Carbon capture and geologic storage to reduce greenhouse gas emissions. Retrieved from U.S. Department of Energy, Office of Scientific and Technical Information. https://www.osti.gov/servlets/purl/1747985
During CO2 injection, pressure and temperature were monitored at the bottom of two observation wells in the AZMI. Scientists and engineers concluded that results validated the concept of AZMI pressure monitoring for leakage detection, but highlighted the need for better engineered and characterized well completions, and improved points for measurement to locate and quantify leakage signals.9Hovorka, S. D., Meckel, T. A., & Trevino, R. H. (2013). Monitoring a large-volume injection at Cranfield, Mississippi—Project design and recommendations. International Journal of Greenhouse Gas Control, 18, 345-360. As with many field projects, results may not only confirm the theory behind new applications of technology, but also focus improvements for better implementation of tools in the future.